Training—whether it’s for technical, sales or soft skills—is a cornerstone of the PHCP industry. Plumbers and HVAC technicians spend much of their time in customer’s homes and businesses troubleshooting, diagnosing, repairing and installing the necessary systems and equipment that keep us healthy, safe and comfortable. Continuing education is vital for these essential workers to keep up with new products, technologies and techniques.
For field personnel, traditional training consisted of in-person classroom instruction coupled with hands-on activities. Online learning opportunities were seen as supplemental at first; recently, however, web training has become a critical component of plumbing and HVAC education.
We’ve seen contractors focus on controlling the controllable.
Today, we are living in the age of COVID-19—a highly infectious respiratory disease ravaging the globe. As of this writing, various sources report 18 million confirmed cases worldwide and nearly 689,000 deaths. The United States has 4.65 million confirmed cases, 157,000 deaths and 2.31 million recoveries. [Source, Wikipedia, The COVID Tracking Project (https://covidtracking.com) and others.]
Associations Step Up
At the beginning of this pandemic, many states enacted stay-at-home orders, allowing only essential workers to be out and about. People were required to work remotely; elementary, high school and college students were required to learn remotely. It was a confusing and chaotic time as businesses and educational institutions shifted awkwardly to the Internet to provide a connection through various virtual meeting applications.
In the plumbing and heating industry, remote learning took on new importance as contractors looked to their association and manufacturer partners for guidance.
“Traditional training content all revolves around a few key areas: how to run a project, how to get paid, how to get work, how to communicate with labor,” notes Brian Helm, current president of the Mechanical Contractors Association of America and president of Mechanical Inc. “With COVID-19, the world was changing; our members wanted to understand what that meant.”
So MCAA changed much of its programming to focus on the impact of the pandemic on its members. It developed its ongoing COVID-19 Contingency Plan Webinar series (https://bit.ly/33ll8ZM) to address these issues and more, including, Helm says: the safety impacts of COVID-19; legal analysis of and training for the federal government’s Paycheck Protection Program (CARES Act); and labor-management issues surrounding the pandemic, such as keeping employees safe on the jobsite and how to staff jobs appropriately.
MCAA called on many of its manufacturers and supplier partners, some of which are Fortune 500 companies, he notes, “to figure out how they were addressing remote work and what their hot buttons were, and then provide training around it.”
“We've been working on virtual content to help our members deal with stagnant air and water systems in closed buildings that are now opening back up for people to work in,” Helm adds. “But probably the most hard-hitting and most valuable resources have been around helping contractors get government help to the extent they need it and also understand what the government provides.”
The Plumbing-Heating-Cooling Contractors-National Association’s Education Committee built the ongoing COVID-19 Recovery Webinar Series (https://bit.ly/2EQ097v) featuring regular “solutions-based content from well-known industry experts to help our members address the challenges they were facing,” PHCC President Jonathan Moyer says. PHCC conducted several contractor impact surveys to “determine challenge areas we could address in our online education.”
Topics included information on federal financial assistance, health and safety requirements, workplace reopening guidelines, customer service and communication, and best financial practices. “If our members can leave these webinars with a nugget or two to help them implement something new and positive for their company, then we have been successful in helping them run their businesses more effectively,” he adds.
Through the PHCC Educational Foundation, the association already had well-established online plumbing and HVAC apprenticeship programs, which were recently upgraded. “When the coronavirus hit, the students were already in the online system, so there were no interruptions,” says Angela Collins, the PHCC Educational Foundation’s senior director of apprenticeship and online training.
She adds that some state associations had not yet transitioned to the new system when stay-at-home orders were enacted. The foundation staff worked on adding more than 100 students to the online roster so the fourth-year students could finish their programs on time.
For non-apprenticeship learning, the PHCC Educational Foundation partnered with Purdue University Professor Kirk Alter to host a weekly live discussion group, Moyer says. The free “Survive and Thrive in Times of Crises” series ran from 10 weeks from March through June.
“The goal was to help contractors stay ahead of the rapidly changing business environment they were facing,” Moyer explains. “The audience was a mix of subcontractors from different trades, plus a few general contractors. This blend helped the group to gain additional perspective on how their peers and trade partners were dealing with jobsite and HR challenges.”
Manufacturers Boost Remote Options
For industry manufacturers, offering factory training as the novel coronavirus rapidly spread across the country was not an option. The challenge was to adapt technical training to complement content already available online.
“Customers were very eager to use their downtime to continue to develop their skills and to explore new products and applications,” says Desmond J. Clancy, the director of sales and customer training at Uponor North America. “Companies were committed to keeping their employees busy; training became a high priority. The big question was, how?
“This industry has historically relied heavily on classroom or conference room-based, instructor-led training in union halls, manufacturing facilities, rep facilities and distribution centers. With that not being an option, we were all forced to seek other ways of offering and consuming training such as e-learning, video, social media and, of course, webinars.”
Mike Licastro, Bell & Gossett/Xylem training and education manager for commercial building services and HVAC, agrees: “The need for remote training was immediate, as contractors wanted to increase their value, engineers needed to maintain training for their licenses and, due to social distancing measures, many nontechnical facility staff quickly realized they were going to become responsible for maintaining the heating and cooling systems in their buildings.”
Manufacturers immediately went to work, developing the needed technical training for newcomers to the industry as well as continuing education modules.
“Although we love to see technicians in person for training, Rheem accelerated the release of innovative digital training content and increased soft skills and technical training,” explains Phil Oglesby, Rheem Mfg.’s manager of education and content development. “For instance, we expanded our Graduate Studies, an online course of study dedicated to soft skills such as sales, sustainability, customer service and the fundamentals of running a business. Additionally, we launched a full catalog of online technical training courses.”
Uponor developed a series of training and sales decks for its factory sales team, rep agencies and distribution to “engage contractors with on-site job training as well as continuing education opportunities,” Clancy says. “We developed content that was easy to deliver in virtual settings such as Zoom or GoTo Meeting. My team facilitated about 60 different webinars from April through June at the peak of the stay-at-home orders and jobsite closures; we are still offering them weekly.”
Uponor also ramped up its social media efforts with a series of live events focused on critical topics to benefit its customers, he adds, as well as increasing the production of how-to videos.
“Bell & Gossett recognized early on that virtual training and opportunities such as live webinars and pre-recorded technical sessions would be our line of communication to contractors during this time,” Licastro explains. “Launching the Bell & Gossett Remote Learning Hub allowed us to consolidate all our training opportunities and materials in one central location, providing industry professionals with easy access. We have completed more than a dozen webinars so far, all with outstanding attendance.”
Through video conference calls, Licastro’s team discusses topics and methods of delivery, including enabling VPN network access so contractors could obtain all the company’s Little Red Schoolhouse training materials remotely.
“Now, more than ever, our skilled labor force has the desire and time to seek additional information and resources to increase their proficiency in the design, installation and troubleshooting of hydronic systems,” he adds.
Uncertainty on the Jobsite
Without a doubt, the construction industry took a blow with COVID-19. While many states considered construction workers and home services providers as essential workers, it was not the case everywhere. Some MCAA members were located in states with more severe restrictions, including construction work stoppages, resulting in canceled jobs that may never come back, Helm notes.
But since states started opening up in May, jobs put on hold are starting up again. “The mechanical industry is at about 80 percent or 90 percent capacity now,” Helm explains. “Productivity has been impacted because we're all trying to work with new PPE and social distancing requirements and making an extra effort to ensure none of our employees become sick.”
Much of the feedback Bell & Gossett received from its contractor customers echoed the same perspective. “If a project did not have an awarded contract or site work had not begun, it was either put on indefinite hold or was canceled altogether,” Licastro notes. “Projects deemed essential were allowed to continue, as long as crews followed all recommended health and safety guidelines required for COVID-19 as issued by the expert governing agencies.”
Initially, he adds, it required a “reduction in workforce, adjusting to remote project management methods and raised concerns about potential financial burden above and beyond contractual costs already accepted before the pandemic.” This concern continues today.
PHCC members were affected by the pandemic, but were able to “quickly adapt to the situation to meet new requirements and protocols,” Moyer says. “While no one is certain of what the future will hold, our members have been busy assessing the current situation and taking steps to be prepared for potential scenarios moving forward. PHCC members are very resilient.”
At the end of March, PHCC Educational Foundation staff notified members of a free pre-apprenticeship course (https://bit.ly/2Xq4iVT; free through the end of the year) in case “people wanted to transition trades or transition jobs or see what other things were out there,” Collins says.
The foundation was flooded with requests from contractor members on the service and repair side who saw work slowing down because of COVID-19 fears among customers. “We only had, maybe, a hundred people enrolled in this course enrolled before March 26; now, we have more than 370 people,” she adds. However, other students dropped out of online courses because work at their companies was hectic.
Industry manufacturers also saw their contractor customers make the changes necessary so their businesses could survive the pandemic and thrive in the aftermath.
“Our customers responded with resilience during these challenging times and focused on the needs of their communities,” Oglesby says. “While every business owner would love to know with certainty how challenges will impact their business, we know it is not possible. We’ve seen contractors focus on controlling the controllable.”
Contractors mobilized teams and implemented procedures so they could continue to serve their customers safely, he explains. “They used unexpected shelter-in-place precautions as a time to re-tool and upskill their teams, utilizing many of the digital training tools Rheem provided,” Oglesby adds. “This proactive approach has positioned contractors to grow despite the challenging environment.”
However, this cautious business optimism does not negate the real anxiety many contractors and their employees have about COVID-19 and the health of their families, friends and colleagues—as well as the economic costs.
“Our customers are concerned about their health and the health of their employees, families and clients but, as essential workers, they are also eager to get to the jobsite to help their customers and our country safely get through this,” Clancy notes. “They are making adjustments on jobsites to ensure everyone is safe and healthy, and the work can get done. But yes, they are most anxious about the uncertainty of the whole situation.”
Helm agrees: “There’s a general level of anxiety, not only at the executive level but at the field level, too, that someone's wife might've been laid off or somebody can't meet their mortgage because they aren't bringing in the income they had. They're fearful that the projects they're still on might get shut down.”
He adds that most MCAA members are seeing the “pipeline of work” slowing down. “Construction is a lagging indicator of the economy,” he says. “We are one of the last sectors to feel a recession—and usually one of the last ones to get out of a recession, too. We have a lot of early indicators we look at. How much are architects able to bill? What kind of engineering has been going on? That's really slowed down. So, most of our members are worried that late fall and into 2021, there're a lot of unknowns.”
Licastro sees it differently: “In most areas, while not 100 percent, workflow is returning to a sense of normal. Any level of anxiety regarding the future is market segment-driven. Depending on where the bulk of a contractor’s work comes from, business course corrections will differ.”
The Future of Remote Training
Regardless of the pandemic, training is vital to an industry that becomes more technology-driven each year. Online training, e-learning, remote education, virtual training—whatever you call it, it’s here to stay.
“Running live training events will continue to be a challenge,” PHCC’s Moyer notes. “A recent survey by the PHCC Educational Foundation showed that even as some employees feel safe enough to attend in-person training, 67 percent of their employers would not currently allow them to get on a plane to fly to a class.”
Uponor’s Clancy notes that investing in remote learning technologies does not take away from in-person training.
“The future of learning and training and education in our industry will be different,” he explains. “Investing in virtual doesn’t mean we want to host fewer people to our training center. The goal is to bring in more people but make better use of that time—less lecture, more practice and more hands-on. But we also are extremely committed to transforming how our industry produces, serves up and consumes training and education to invest in the professionals we support every day. This is a strategy we were committed to long before COVID-19 and one we are even more committed to today.”
Uponor is developing other types of remote training such as e-learning, microlearning, on-demand video tutorials and other digital job aids to provide contractors with information when and how they need it. “We are also exploring technologies such as virtual reality and social learning platforms that are transformational opportunities,” Clancy adds.
The nature of the labor force will influence future training in the industry, Rheem’s Oglesby notes.
“Students want to learn new material in digestible, smaller chunks of related information, especially during online courses,” he says. “Additionally, given the labor shortage faced by our industry, it can be difficult for a contractor to commit to full-day training for their technicians. Going forward, I do think there will be an increase in remote/online learning in the years to come. We can foresee a future with a hybrid approach, utilizing the best of both in-person and digital learning.”
Rheem recently partnered with Interplay Learning to offer online technical training content, including customized, three-dimensional and virtual reality content, he adds: “This technology is being adopted by many skilled trades to replicate a hands-on training experience in a small, portable form.”
Collins agrees virtual learning is perfect for the new generations of plumbers and HVAC techs. “I think this generation of up-and-coming plumbing apprentices are intellectually curious and technology-savvy,” she says. “If there was a group to do online, remote technical work, this is the group to do it with—because this is how they're learning. We're speaking their language.”
The PHCC Educational Foundation is working on fast-track service plumbing modules, creating smaller, more digestible courses—such as plumbing math, construction math, pipes or plumbing for non-plumbers.
“We believe in online learning,” Collins says. “A hundred percent of my career has been devoted to the fact that we need to make education accessible to everybody. And a lot of people, even pre-COVID, had family issues such as eldercare or childcare issues to deal with. Sitting in class for four hours every night is unfeasible. I think the pandemic has allowed people to see that remote learning has a purpose.”
However, live, in-person training is truly the lifeblood of the PHCP industry, and Bell & Gossett doesn’t expect that to change, Licastro says.
“While we fully expect remote learning to play a more prevalent role in the future of training, we do not expect the demand for in-person training to decline dramatically,” he states.
As the company hosts hydronic systems webinars, offers self-paced virtual training for CEU credit through the Online Little Red Schoolhouse, and adds digital materials to its Remote Learning Hub, Bell & Gossett is looking to a post-COVID-19 era.
“Our next step is to use the audio and visual capabilities of the Little Red Schoolhouse to their fullest by hosting live training events,” Licastro adds. “Students can see the instructors presenting the material on screen, and we can run the system demonstration stations in real-time as well. Making these improvements will provide a remote learning experience that more closely resembles in-person training.”
But it’s the connections, the networking, the life-long friendships developed over two or three days of intensive instruction—part of the human experience—that can never be replicated by a laptop, tablet or smartphone.
“One of the best benefits of in-person training is face-to-face collaboration,” MCAA’s Helm says, “A lot of our programs in the past were built around connections people make at events. Virtual training is always going to be part of the equation, but I don't see us going to an exclusively virtual situation in the long-term.”
Kelly Faloon is a contributing writer to CONTRACTOR magazine. The former editor of Plumbing & Mechanical magazine, she has more than 30 years’ experience in B2B publishing; 22 of those years were spent covering the plumbing, heating, cooling and piping industry. A native of Michigan’s northern Lower Peninsula, Faloon is a journalism graduate of Michigan State University.
About the Author
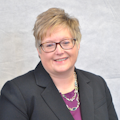
Kelly L. Faloon
Freelance Writer/Editor
Kelly L. Faloon is a contributing editor and writer to Contractor, Contracting Business magazine and HPAC Engineering and principal of Faloon Editorial Services. The former editor of Plumbing & Mechanical magazine, Faloon has more than 26 years of experience in the plumbing and heating industry and more than 35 years in B2B publishing. She started a freelance writing and editing business in 2017, where she has a varied clientele.
Faloon spent 3 1/2 years at Supply House Times before joining the Plumbing & Mechanical staff in 2001. Previously, she spent nearly 10 years at CCH/Wolters Kluwer, a publishing firm specializing in business and tax law, where she wore many hats — proofreader, writer/editor for a daily tax publication, and Internal Revenue Code editor.
A native of Michigan’s northern Lower Peninsula, Faloon is a journalism graduate of Michigan State University. You can reach her at [email protected].