For decades, modular construction has been touted as the next “revolutionary” wave of construction. Instead of putting together structures on a jobsite, where workers are subject to the vagaries of the weather, workers build modules in climate-controlled buildings and with readily accessible tools and materials. Productivity rises, as do project savings.
“The appeal of the full modular system is understandable,” a Harvard Business Review article notes. “The architectural design is coordinated with factory engineers and technicians, every individual element in the plans is digitized, pieces are machine pre-cut and fitted to exact dimensions, sub-assemblies are moved from station to station by conveyor or overhead crane, and the entire process takes place in a comfortable setting free from Mother Nature’s whims.”
The Modular Building Institute’s (MBI) 2023 Permanent Modular Construction Report notes that the modular industry “topped $12 billion in North America in 2022, accounting for 6.03% of all new construction starts.” This market percentage is nearly triple what it was in 2015. Also, this is the third consecutive year that the multifamily market topped the industry: 21% in 2020, 24% in 2021 and 32% in 2022.
Modular’s benefits include reduced safety hazards, jobsite waste, dependence on skilled labor, and materials/labor costs, notes the American Institute of Architects (AIA): “Modules are oftentimes fabricated while the building site is being prepared, which can cut the time in half compared to traditional construction methods… Barring shipping delays or poor planning, modular construction can help save time, project delays and weather uncertainty.”
Safety is the No. 1 concern on all construction sites, yet modular construction removes the No. 1 cause of construction deaths: falls. A 2020 Dodge SmartMarket report on prefabrication and modular construction notes that nearly 90% of respondents agreed that modular provides a safer workplace.
The promise of modular seems to be just what the industry is looking for, especially considering the ongoing skilled trades labor shortage. Even during the COVID-19 pandemic, modular builders were able to keep employees at safe distances because of the nature of the work. However, going forward means clearing some significant hurdles.
Roadblocks and Misconceptions
The AIA also mentioned a few drawbacks to modular construction: quality control, skilled labor for installation on the jobsite and financing. Issues attributed to quality control include possible defects in prefabrication, and the damage risk during transportation from the factory to the jobsite.
“Despite promised cost savings, environmental benefits and quicker return on investment, contractors are still running into roadblocks using modular construction,” notes a ConstructionDive article. “Many face a steep learning curve, and there can be snafus with design, manufacturing, transportation and assembly, they say.”
That learning curve—for general contractors, subcontractors and engineers—requires the unlearning of decades of construction knowledge while retraining workers how to monitor quality and track progress. “The methods are so dissimilar and used so infrequently that it can be difficult for contractors and subs to get into a cadence,” the article says.
An additional explanation involves the historical, negative stigmas of modular-constructed buildings as cheap, low quality, cookie-cutter structures that are not built to last.
“Aligning with these misconceptions, modular construction is rarely viewed as an alternative or substitute for stick-built construction,” says Meg Dowaliby, lead copywriter at Pacific Mobile Structures, in an MBI post. “Many end users fail to realize that it does, in fact, achieve results that rival stick-built and, in many cases, surpass it.”
Technology and Timelines
Most in the construction industry agree that the introduction of building information modeling (BIM) has only helped the modular construction concept. The increasing use of this and other technologies—3D printing, digital twins, augmented and virtual reality—“will streamline processes and enhance project efficiency.”
Multifamily, healthcare, hotels and education projects “lent themselves to an assembly line orientation because they had repetitive design concepts and offered economies of scale based on consistent software programming and the constant repetition of tasks on the shop floor,” notes the Harvard Business Review.
McKinsey & Co.’s analysis notes that going modular could allow “home builders to accelerate end-to-end project timelines by 20 to 50[%] while reducing costs by up to 20[%]. Moreover, modular projects may be easier to execute on urban [jobsites] since they require less space for the storage and preparation of materials.”
Other countries have seen much better market penetration—nearly half (45%) of current housing stock in Finland, Norway and Sweden use modular construction. Japan’s modular construction market is 15% of homes, with the United States coming in at less than 4%.
However, the industrialization of the building industry can turn some construction professionals off as it commoditizes projects.
“Modular players need best-in-class manufacturing capabilities, including sophisticated digital design platforms and lean, efficient production lines,” McKinsey & Co. explains. “As a result, modular construction companies often think of themselves first and foremost as design and technology companies. That difference is clear in the way these businesses present themselves to potential customers.
Green Construction and Gen-Zers
Regardless of these challenges, modular construction does have its place in the US building industry, and the market is expected to continue to grow. How can modular construction advocates convince US construction professionals to capitalize on these opportunities?
One method is to appeal to the end-user, MBI explains: “The advantages of modular construction ring loud and clear to developers, builders and general contractors. However, the end user—whose opinions drive stigmas and beliefs about modular construction, doesn’t have a direct line of sight as to its advantages and how they add value for them.”
For affordable housing advocates, modular’s cost reductions and other benefits makes it ideal for providing “affordable, sustainable and resilient” housing.
“Modular building, if brought to scale, has the potential to reduce construction costs and make it more affordable to build new homes, especially in areas experiencing severe affordable housing shortages.,” notes the Center for American Progress. “Most importantly, modular building can deliver housing quickly to meet the needs of cost-burdened individuals and families who would otherwise be displaced or become homeless.”
The promise of sustainable and resilient can also attract younger generations that prioritize a greener way of life. Two environmental benefits of modular buildings fit this bill—a smaller footprint and greener construction practices.
“This future of construction and design is already welcomed with open arms by millennials and now, Gen-Zers,” MBI explains. “These generations have embraced ‘van life’ and tiny home living—simultaneously out of necessity and a more environmentally mindful and conscientious lifestyle. These next generations could drive the future of construction toward modular.”
Kelly Faloon is a contributing writer to CONTRACTOR magazine and principal of Faloon Editorial Services. The former editor of Plumbing & Mechanical magazine, she has more than 35 years of experience in B2B publishing, with 26 of those years writing about the plumbing, heating, cooling and piping industry. Faloon is a journalism graduate of Michigan State University. You can reach her at [email protected].
Modular Advocates Unite
Last fall, the Modular Building Institute (MBI) launched a multiyear, multimillion-dollar campaign to “spur investment and promote greater adoption of modular construction.” Its focus will be on these key areas:
• Influencing government legislation, regulations, procurement, programs and codes.
• Creating new business opportunities for the industry.
• Expanding outreach efforts to developers, architects and code officials.
• Attracting new employees to the industry, including nontraditional workers.
“I expect to see a big uptick in the number of women, minorities and young people in our industry over the next five years as we roll out this campaign,” says MBI Executive Director Tom Hardiman. “I think people who otherwise would not consider a career in traditional construction will want to be a part of a transformative industry like ours.”
In addition, MBI hosts modular industry professionals this month in Orlando, FL, at its annual World of Modular.
About the Author
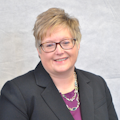
Kelly L. Faloon
Freelance Writer/Editor
Kelly L. Faloon is a contributing editor and writer to Contractor, Contracting Business magazine and HPAC Engineering and principal of Faloon Editorial Services. The former editor of Plumbing & Mechanical magazine, Faloon has more than 26 years of experience in the plumbing and heating industry and more than 35 years in B2B publishing. She started a freelance writing and editing business in 2017, where she has a varied clientele.
Faloon spent 3 1/2 years at Supply House Times before joining the Plumbing & Mechanical staff in 2001. Previously, she spent nearly 10 years at CCH/Wolters Kluwer, a publishing firm specializing in business and tax law, where she wore many hats — proofreader, writer/editor for a daily tax publication, and Internal Revenue Code editor.
A native of Michigan’s northern Lower Peninsula, Faloon is a journalism graduate of Michigan State University. You can reach her at [email protected].