MCAA President Robert Bolton: Strengthening Labor Relations
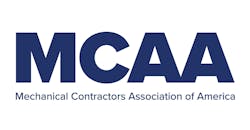
In March, the Mechanical Contractors Association of America presented a new president to its members: Robert Bolton, CEO and president of Pawtucket, R.I-based Arden Building Cos. The full-service mechanical, sheet metal and electrical contractor offers engineering design, construction and maintenance services.
Bolton serves as president of the New England MCA, is on the board and works with the group’s Industry Improvement Fund. He chairs the Collective Bargaining and Labor Management Committees for UA Local 51 and the IBEW Local 99 in Rhode Island. In addition, he is the co-chairman of the UA Local 51 Pension Annuity Plan and for the IBEW Local 99 Pension Annuity Plan.
After attending a Mid-Year Education Conference, Bolton served the national MCAA on its Project Managers Education and Management Methods Committees. He was also a facilitator for MCAA’s Advanced Institute for Project Management.
Bolton was elected to the MCAA board in 2015. He currently serves on the Education Committee and the Industrial Relations Council, and is a 2016 graduate of MCAA’s Advanced Leadership Institute Program.
We spoke to Bolton about his love of the mechanical industry, his hopes to strengthen labor/management relationships, and a focus on increasing education and training opportunities for smaller plumbing and mechanical contractors.
How did you know you wanted to be part of this industry? How did you get your start?
What do you love about your job? What do you not love about it?
RB: At this stage of my life, I enjoy making sure our company is financially sound so our employees can feel secure about their employment. There isn’t anything that I don’t love about my job because I truly love what we do in this industry.
What piece of advice helped you the most in your career?
RB: My father always said, “Never build a monument.” In other words, know when to walk away from a bid.
What are you most passionate about in the industry? How do you hope to work on this issue while MCAA president?
RB: Healthy labor/management relationships are so important to the success of our industry. As president of MCAA, I will continue to partner with UA General President Mark McManus to strengthen the MCAA-UA relationship.
I will also reach out to our other labor partners across the United States because we, as MCAA contractors, need to be able to work closely and harmoniously with them, too — just as we have with the UA for years now.
As we continue to deal with the COVID-19 pandemic, what are the top three problems facing mechanical contractors today? How is MCAA helping members with those issues?
RB: While I think the pandemic is largely behind us, we face challenges with inflation, worker shortages and supply chain interruptions. Given the recent geopolitical events in Eastern Europe, these challenges are likely to continue into the foreseeable future.
MCAA is working closely with the UA to identify the needs of our clients and contractor base. Together, we are developing programs such as MCAA’s Field Leaders Conference, supporting all the Joint Apprentice and Training Committees across the country, and enhancing our educational programs for project managers and executives.
How are members using technology to navigate the COVID-19 landscape during project planning and on jobsites?
RB: While most of the safety protocols are being lifted, we must comply with those that are still in place to ensure the safety of our clients and workforce. I think everyone has become an expert in online meetings at this point.
Beyond that, contractors are reducing the onsite workforce and using prefabrication, new tooling and innovative products. Performing as much work as we can in a controlled environment creates a safer workplace for our workers while increasing productivity in the field.
MCAA members are also using technology to give project managers and designers the ability to look at a jobsite without being there in person. This can be as simple as apps that communicate project status or as complex as capturing weekly scans with 360-degree cameras and software that document work and provide status updates. This technology has real cost and labor productivity impacts, and we must build those into our estimates.
What technologies are building owners requesting now that many people are going back to in-office work?
RB: Coordination meetings using any number of live video platforms are not going away. Using these platforms requires upgrades to Internet connections, cybersecurity and the latest mobile devices. COVID-19 also allowed owners to switch over to digital project management platforms out of necessity. As they start using new software, so do we.
How do members feel about in-person industry events?
RB: MCAA members are ready to get back to in-person industry events. Our safety and technology conferences and our annual convention all sold out in record time.
We have found there’s still a market for online learning as well. The new Preparatory Institute for Project Management has helped meet that demand, along with virtual versions of our National Education Initiative courses. Beyond that, we have more than 670 resources on www.mcaa.org for our members to download as a free membership benefit.
What safety issues are members most concerned about? How is MCAA helping?
RB: For the last few years, MCAA members’ chief safety concern was navigating the evolving COVID-19 rules and instituting practices to keep workers safe. That’s still a concern in some areas, but the focus is shifting to other issues.
Today, MCAA and our members are focused on making sure that Occupational Safety and Health Administration guidelines regarding heat injury and illness prevention protect workers and are easy for contractors to implement. MCAA is working with our industry partners and OSHA to propose simple guidelines that meet that goal.
MCAA members are also focused on safety and health training. Our organization offers hundreds of safety resources to support their needs, including training videos on topics such as silica dust, fall prevention, personal protective equipment, ergonomics and the safe use of power tools. It’s no wonder that MCAA members continue to outperform the industry when it comes to recordable cases and lost workday cases.
What are the top three regulatory or legislative issues affecting the industry? How is MCAA advocating for its member on those issues?
RB: Legislative and regulatory developments impacting work opportunities are our members’ key concern—and MCAA’s top priority. Public infrastructure measures, the government’s Federal Green Building initiative, and shifts in private sector project types and technological approaches all present opportunities.
Issues related to labor standards and workforce sufficiency are another big concern for MCAA and our members. Together with the UA, MCAA works to maintain high labor standards because our customers demand and deserve them.
Likewise, our workforce and their families deserve to be protected, so MCAA works for constructive changes in prevailing wage protections for our markets, and advocates against employee misclassification that hurts our workforce and our businesses.
MCAA is always on the lookout for well-intentioned sounding reforms, such as the recent apprenticeship expansion proposal, to make sure they don’t present unrealistic challenges for our contractors and the industry overall.
What training/education initiatives will MCAA focus on in 2022?
RB: Through our training and educational programs, MCAA member contractors can attend classes facilitated by industry leaders who bring their experience and advice to each encounter.
MCAA thrives on delivering educational programs that help its members to compete. We need to do more for our smaller mechanical and plumbing contractors. Their growth depends upon having as many learning opportunities and open doors as we can provide.
This year, as MCAA’s president, I intend to broaden our outlook even more and make small-contractor education one of the key elements that will drive our MCAA agenda.
How can mechanical contractors and engineers collaborate better to ensure the best project outcomes?
RB: Our most successful projects are ones where the design team is at the table with us during the building information modeling process—resolving routing conflicts, reviewing issues with submittals, answering Requests for Information and reviewing change orders. These areas of a project are time-sensitive to the overall successful outcome of a project; working together to resolve them helps speed things along.
Are you optimistic about the future of the mechanical industry?
RB: I truly believe the future of our industry across the mechanical/electrical/plumbing trades is so exciting. Our dependence on overseas manufacturing of so much of what we depend on cannot continue.
The microchip shortages, medical-grade glass for vials or all the N-95 masks that we needed during the pandemic are a few examples that we can all relate to. Industries are now bringing back manufacturing to the United States and addressing clean energy.
If you only had one message to give to your fellow contractors, what would it be?
RB: Hire the best employees out there and invest in their development and training.
Anything to add?
RB: I want to thank the MCAA, the board of directors and the employees of the Arden Building Cos. for the opportunity and support to serve as president of one of the finest trade organizations across the country.
Kelly Faloon is a contributing writer to Contractor, Contracting Business and HPAC Engineering magazines, and principal of Faloon Editorial Services. The former editor of Plumbing & Mechanical magazine, she has more than 20 years of experience in the plumbing and heating industry and more than 30 years in B2B publishing. Faloon is a journalism graduate of Michigan State University. You can reach her at [email protected].
About the Author
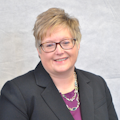
Kelly L. Faloon
Freelance Writer/Editor
Kelly L. Faloon is a contributing editor and writer to Contractor, Contracting Business magazine and HPAC Engineering and principal of Faloon Editorial Services. The former editor of Plumbing & Mechanical magazine, Faloon has more than 26 years of experience in the plumbing and heating industry and more than 35 years in B2B publishing. She started a freelance writing and editing business in 2017, where she has a varied clientele.
Faloon spent 3 1/2 years at Supply House Times before joining the Plumbing & Mechanical staff in 2001. Previously, she spent nearly 10 years at CCH/Wolters Kluwer, a publishing firm specializing in business and tax law, where she wore many hats — proofreader, writer/editor for a daily tax publication, and Internal Revenue Code editor.
A native of Michigan’s northern Lower Peninsula, Faloon is a journalism graduate of Michigan State University. You can reach her at [email protected].