For the company's 85th anniversary in 2021, Freeborn Mower Electric Cooperative in Albert Lea, MN, decided to build a new facility to house all its equipment, trucks and employees in one location. The new 97,000-sq.-ft., $17 million structure featured several high-tech, sustainable building practices, including radiant floor heating throughout the entire building.
Being an electric co-op serving 21,045 members in two counties with 2,950 miles of line, Freeborn wanted the most energy-efficient method for heating its structure, which meant a radiant floor heating system.
“The co-op purchased an 80-acre site,” explains Taylor Bestor of Valor Mechanical (Stewartville, Minn.), the radiant contractor. “The in-floor heat ran off of a water-to-water heat pump system with geothermal. Minnesota geothermal contractor GeoSystems drilled almost 300 wells north of the building, circulating water through a buffer tank and multiple zones. Three ClimateMaster geothermal heat pumps also ran the Mitsubishi variable refrigerant flow system.
“And nearly 30 fan-coil units provided cooling to some warehouse rooms and all the offices in the building.”
Valor Mechanical
Bestor has been installing commercial systems since 2007. “Radiant heating is pretty popular in Minnesota,” he notes. “Anyone who has it greatly appreciates it and highly recommends it. For those hesitant about the upfront cost, we strongly recommend they at least get the tubing in the concrete. They're usually grateful they did it.”
At the Freeborn site, the Valor Mechanical crew used Wirsbo hePEX pipe for the radiant floor heating system and Ecoflex pre-insulated piping to the TruFLOW manifolds for the underground distribution system.
Bestor had always used traditional methods of wire ties or foamboard staples; however, the engineer’s specification called for Uponor’s Radiant Rollout preassembled mats for the warehouse. He was curious about how the installation would go, knowing he needed to align with concrete-pour schedules to stay on the customer’s tight timeline.
Staying on Schedule
“I always have concerns about fitting in the concrete,” Bestor says. “However, the mats came with air testing. So I knew that all the joints were good because once we cut the test fitting off, it would release all the air in it. I have a pretty good understanding of how the in-floor heat loops work, and it had a reverse return on it, which is the way I prefer to pipe my hydronics. It worked out really well.”
Each mat was 150 feet long with three tubing loops; the crew installed 34 mats with 11 manifolds in the warehouse. The radiant perimeter used a staple-down method. Bestor explains that the space was separated into three zones: the north side of the warehouse, the south side, and a wash bay that was controlled separately
Uponor’s Paul McCulloch and Swanson were there for the first install to guide Bestor and his team with the mats. The crew planned to complete the radiant tubing install in thirds to work with the concrete pours.
Bestor employs 15 field installers, five service techs and five office personnel.
“With the Freeborn project, we started training about 10 guys to understand how the mats worked,” he explains. “Once we started, we were able to knock out 15,000 to 20,000 square feet in just a day. By the last third of the project, we could do the entire install with three guys in one day. Using traditional wire ties or staples would have taken more than double the workers and triple the time.”
Working Through a Pandemic
“The general contractor implemented a mask policy at the time, and it was a large enough jobsite that it was pretty socially distant,” Bestor recalls, adding that there were some cases, but they didn’t adversely affect the project.
Throughout much of the country, construction workers and home service contractors were deemed essential to keep as many construction jobsites as possible open and working toward completion.
Today, Bestor’s radiant business is going strong. And as he avails himself of all the industry’s technology and time-saving products and equipment—teaching his installers and service techs along the way—he promotes professionalism to his staff, which gives them confidence on the jobsite. This confidence, and radiant floors, makes his customers more comfortable.
Kelly Faloon is a contributing writer to CONTRACTOR Magazine and principal of Faloon Editorial Services. The former editor of Plumbing & Mechanical magazine, she has more than 20 years of experience in the plumbing and heating industry and more than 30 years in B2B publishing. Faloon is a journalism graduate of Michigan State University.
About the Author
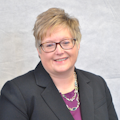
Kelly L. Faloon
Freelance Writer/Editor
Kelly L. Faloon is a contributing editor and writer to Contractor, Contracting Business magazine and HPAC Engineering and principal of Faloon Editorial Services. The former editor of Plumbing & Mechanical magazine, Faloon has more than 26 years of experience in the plumbing and heating industry and more than 35 years in B2B publishing. She started a freelance writing and editing business in 2017, where she has a varied clientele.
Faloon spent 3 1/2 years at Supply House Times before joining the Plumbing & Mechanical staff in 2001. Previously, she spent nearly 10 years at CCH/Wolters Kluwer, a publishing firm specializing in business and tax law, where she wore many hats — proofreader, writer/editor for a daily tax publication, and Internal Revenue Code editor.
A native of Michigan’s northern Lower Peninsula, Faloon is a journalism graduate of Michigan State University. You can reach her at [email protected].