Anyone who’s been on a construction site knows that traditional construction methods are inefficient, time-consuming and costly. At each step, productivity is lost as crews wait for each other before they can move on to the next level. Delays caused by miscommunication — either on the jobsite or in the design process — routinely throw off the construction schedule, which costs time and money.
For such reasons, some in the plumbing and mechanical industry have long been proponents of prefabrication and modular construction. Now, however, the time to shift to off-site manufacturing-style production on a large scale finally seems at hand.
“While modular (or prefabricated) construction is not a new concept, it is attracting a fresh wave of interest and investment on the back of changes in the technological and economic environment,” stated a 2019 report from management consulting firm McKinsey & Co. “Recent modular projects have already established a solid track record of accelerating project timelines by 20 to 50%.”
Entitled “Modular Construction: From Projects to Products,” the report also noted the construction method can cut project costs by 20%. In this sense, modular refers to three-dimensional volumetric building components comprising entire buildings.
“The primary advantage is the speed of the construction and quicker occupancy for the owner or the end-user,” says Tom Hardiman, executive director of the Modular Building Institute, a post he’s held since 2004. “That’s the big driver, why it’s gaining so much traction with multifamily developers, with hotel and hospitality developers. They can generate revenue much quicker.”
On a conventional, site-built project, the carpenters come in first, then the electricians, then the plumbers and HVAC techs, then the drywallers, then the painter, and then the tiler. “It’s all very sequential,” Hardiman explains. “In a factory, all those trades are there and working together. When that box, that room, comes out of the factory, it could be 80% complete. Electric, plumbing, paint, carpet, drywall, everything.”
For Roger Krulak, president and founder of Brooklyn-based FullStack Modular, the volumetric modular building method (six-sided modules instead of prefabbed panels) seems the most logical way to build.
“It’s an integrated, logical solution because it’s process-focused,” he says. “It has to be accurate, complete and coordinated. We all know in this industry that even if you are an all-BIM shop, it doesn’t mean it’s a coordinated process with every other discipline. But in our solution, it’s the only choice — everything fits before it leaves the factory. Modular construction is incredibly efficient, and it allows you to take advantage of the economies of process.”
Labor, Environmental Pluses
Another significant advantage concerns workforce issues, Hardiman adds. In remote areas where there is not an adequate construction workforce, building modules in a factory and then transporting them to the jobsite is more cost-effective. Or the project may be in an urban area where labor costs are high, so modular construction could save on those costs.
Also, the environmental advantage to building via modular is the significant reduction in the amount of construction waste. “You’re wasting much less material because these factories are ordering their construction materials in bulk,” Hardiman explains. “Whatever they don’t use for a particular project, it stays in their inventory. It doesn’t end up in the landfill as it does on a site-build project.”
So, clients with sustainability missions have shown growing interest. Krulak’s firm focuses primarily on the $63-billion market consisting of multifamily, lodging, student housing and affordable housing.
“Our envelope and our units and our modules have tolerances of a quarter-inch or less across all systems,” he says. “They’re incredibly tight. And we can build modules as sustainable as you want them. We’re building some passive housing, and using other green building methods. Most of our customers nowadays are either using a VRV system or a heat pump system.”
One final advantage that is always a concern in construction but maybe more so now, as the COVID-19 pandemic continues: worker safety.
“Because these workers are in the factory, they’re in a controlled setting,” Hardiman explains. “They’re working on the ground floor, even if they’re building modules for the second, third, 10th, or 30th floor of a building. It virtually eliminates fall protection risks. And what we’re finding with COVID now is that it’s much easier to manage and control a factory setting with social distancing and staggered shifts than it is a traditional jobsite.”
Still, according to McKinsey & Co., one disadvantage for designers in a modular world comes as “onsite construction may become a smaller and more commoditized part of the value chain. [But] traditional engineering and construction firms can counter this risk by moving into development, consulting and planning.
And the pivot doesn’t have to stop there. “[Developers] can also aggressively make use of modules to gain margin advantages over competitors for what looks to be an extended transitionary period. Finally, they can focus on highly complex projects that demand more onsite work, since custom projects will not disappear,” the report concluded.
Economies of Process
“Modular construction requires different design thinking to account for production efficiencies, opportunities to develop standardization to offer mass customization, and ease of transport and assembly,” the McKinsey & Co. report noted. “All of this has to work within the same mandate that always governs construction projects: creating pleasing and functional spaces for the eventual occupants. The right design can improve productivity by 3 to 12 percent.”
Building information modeling (BIM) is a perfect complement to volumetric modular building, Hardiman says, although many modular builders are not using it. MBI has about 420 member firms, but only a quarter use BIM regularly on projects.
“It’s one of those tools that if you combine it with modular construction, you’re going to get an exponential efficiency instead of just using one or the other,” he notes.
Upfront, early communication with the entire team — owner, general contractor, architect, engineer, the modular manufacturer — is absolutely critical, Hardiman adds. “Get them all together and lay out the scope clearly because it is a different way of constructing buildings. You don’t want to assume the GC is going to do something when the modular manufacturer was going to do it, and vice versa. So the use of BIM is helpful, regardless of what other tools or technology are used.”
Regarding the installation process, Krulak adds: “The economies of process of doing something in the correct order, in lieu of what we call the parade of trades, is a huge advantage. We get somewhere around seven to seven and a half hours of productivity in an eight-hour day.”
All systems are tested, just as they would be on a site-built project. So once modules are delivered to and placed on the jobsite, all that’s left for the crew is to make final plumbing, heating and electrical connections.
“Modular construction makes sense if you’re building anything that has any kind of repetitive nature, where the same workers are working on the same type of product multiple times, similar to assembly workers in a car factory,” Hardiman explains.
Educating for Growth
Last year, MBI worked with the American Institute of Architects (AIA) to develop the “Modular and Off-Site Construction Guide” (www.aia.org/resources/6119840-modular-and-off-site-construction-guide) as a primer for designers on permanent modular construction. It explains the value and opportunities of modular design, the pitfalls designers should be wary of, and offers case studies from multiple market types.
The guide comes at a time when the modular construction industry is gaining market share. In the U.S., MBI puts modular construction’s share of the new construction market at about 4%. “That number has almost doubled in the last five years,” Hardiman says. “It was about 2.3% five years ago. So, 4% may not sound like a lot, but the industry has grown from just under $5 billion in the value of new projects put-in-place to more than $9 billion.”
And COVID-19 may push those numbers up even higher.
“The same problems exist,” he explains. “We still have a shortage of affordable housing. We still have a shortage of skilled construction labor. We have educational facilities that dramatically need upgrading. We have healthcare infrastructure needs to be addressed,” adds Hardiman.
“There’s going to be no other way to meet all of this infrastructure demand without moving to some form of industrialized construction process,” he predicts. “We just don’t have the labor to build it conventionally. So, I think it’s inevitable that our industry will grow.”
About the Author
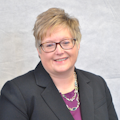
Kelly L. Faloon
Freelance Writer/Editor
Kelly L. Faloon is a contributing editor and writer to Contractor, Contracting Business magazine and HPAC Engineering and principal of Faloon Editorial Services. The former editor of Plumbing & Mechanical magazine, Faloon has more than 26 years of experience in the plumbing and heating industry and more than 35 years in B2B publishing. She started a freelance writing and editing business in 2017, where she has a varied clientele.
Faloon spent 3 1/2 years at Supply House Times before joining the Plumbing & Mechanical staff in 2001. Previously, she spent nearly 10 years at CCH/Wolters Kluwer, a publishing firm specializing in business and tax law, where she wore many hats — proofreader, writer/editor for a daily tax publication, and Internal Revenue Code editor.
A native of Michigan’s northern Lower Peninsula, Faloon is a journalism graduate of Michigan State University. You can reach her at [email protected].